
Embodied Carbon in Vancouver Building Bylaw 2025
July 9, 2024
Cost-Neutral Embodied Carbon Reduction Strategies for Residential and Commercial Buildings
October 7, 2024
Written by Forest Borch, Martina Soderlund, and Hugh Nolan, reLoad Sustainable Design. All images courtesy of reLoad Sustainable Design unless otherwise noted.
The City of Vancouver's Climate Emergency Action Plan aims for a 40% reduction in embodied carbon in new buildings by 2030 (compared to a 2018 baseline) and to halve their operational emissions, also by 2030 (compared to a 2007 baseline). Reflecting this commitment, the City of Vancouver adopted these targets into the Owner Project Requirements (OPR) of the new Marpole Community Centre. Meeting these ambitious objectives demanded unwavering commitment and a high degree of collaboration from the owner, design team, and general contractor throughout the design phase.
The Building
The Marpole Community Centre is a new, 6,100 m2 community centre that will be constructed in Oak Park, Vancouver. The building will replace the existing 80-year-old facility to better serve the community in one of Vancouver’s fastest growing neighbourhoods. The community centre includes a gymnasium, fitness centre, field house, and multi-purpose rooms, as well as a 74-space childcare facility on the second floor. There will be one level of underground parking.
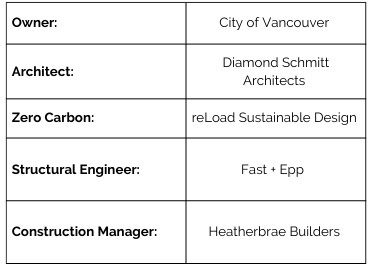
Ambitious Performance Goals
The Marpole Community Centre will be the first community centre built by the City of Vancouver in the last decade. The City’s goals are to build the most inclusive and high-performance facility the City has ever built.

Aerial view of the Marpole Community Centre in Oak Park. Image by Diamond Schmitt Architects, Vismo and Andrew Fyfe
For this project, the City is applying a holistic approach to emissions reductions, targeting not only a 40% reduction in embodied carbon, but also near-zero operational emissions with 100% electric systems, Passive House certification, and LEED Gold certification. The OPRs also include climate resilience, Rick Hansen Foundation Accessibility certification (gold) and consultation with the Indigenous community so that Host Nation artwork and concepts can be meaningfully incorporated into the design.
Setting the Baseline
With an ambitious project goal to reduce embodied carbon by 40%, developing a baseline for comparison was key to designing the building. However, at the beginning of the design phase, the method for defining the baseline was ambiguous. The project team collaborated with the City to work toward a common understanding of the project baseline.
Mid-way through the design phase, the project team adopted the preliminary draft version (2022) of the City’s Embodied Carbon Guidelines (ECG), serving as a pilot project to test the guidelines. As the design progressed, the design team provided feedback to the City regarding methods for achieving reductions in embodied carbon and the corresponding methodologies for substantiating them.

Rendering of the Marpole Community Centre
Once the City published the first version of its ECGs in October 2023, the project’s whole building life cycle assessment (wbLCA) was updated to align with the ECGs. This included ensuring functional equivalence between the baseline and the proposed design as follows:
Geometric Equivalence
The building layout, column spacing, building areas and window-to-wall ratio were kept the same between the baseline and proposed design. The ECGs allow geometric differences for the parkade so that the project can take credit for a ‘lighter and smarter’ design.
Structural Equivalence
The structural performance between the proposed hybrid mass-timber superstructure and the baseline’s steel superstructure was the same, including the fire ratings for structural elements.
Thermal Equivalence
The clear-field R-values of the building enclosure and the number of panes of glazing were maintained between the proposed and baseline designs.
Contribution Analysis
To pinpoint the building elements with the greatest impact on the project’s embodied carbon, a contribution analysis was conducted. It allowed the design team to target embodied carbon reductions for specific building elements during the early stages of the design process.
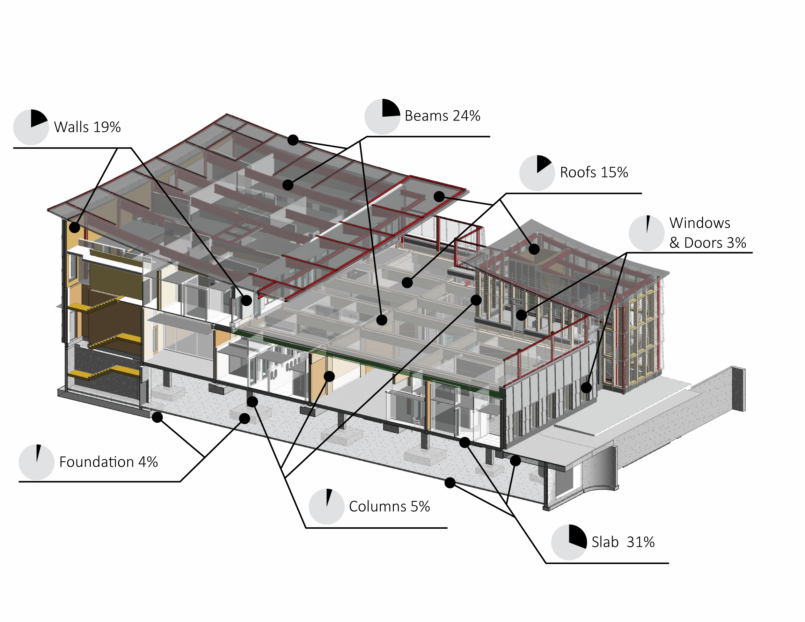
Section view through the project Revit model with callouts showing the relative embodied carbon of the building elements at the building permit stage
Five Lessons Learned
1. Review Massing and Grid Layout
Diamond Schmitt Architects coordinated all consultants and organized team and breakout meetings throughout each phase of the design process. Three early-stage schematic design options were evaluated for their embodied carbon impact, along with other design parameters, to give direction on building massing.
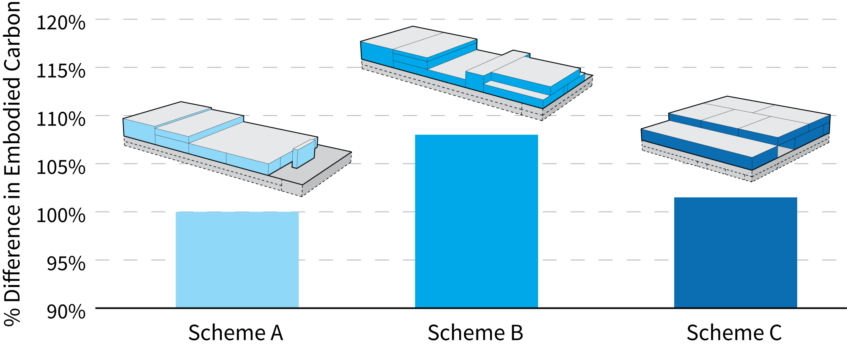
Three early-stage schematic design options considered by the project team
Early-stage embodied carbon analysis informed the choice to proceed with Scheme A. From there, an early-stage design meeting between reLoad Sustainable Design, Fast & Epp, and Diamond Schmitt Architects set the project structure on a rigid grid for an efficient, mass timber-friendly structure.
2. Enable a Mass Timber Structure

The applicable version of the Vancouver Building Bylaw (VBBL 2019) lacks provisions for a building of this size and occupancy classification to be built using combustible construction, thereby prohibiting the proposed mass timber structure. To overcome this limitation, the design team worked with the City to compartmentalize the gymnasium from the rest of the building using a two-hour fire-rated partition. Additionally, the exiting capacity for the gymnasium and the community centre were independently addressed to ensure occupant safety in the event of an evacuation. Through this compartmentalization process, the remaining community centre building area was brought within VBBL limits, allowing for the use of a combustible, mass timber hybrid structure.
3. Reduce Below-Grade Parking

The Vancouver Bylaw initially required 174 parking stalls for the community centre. Because the project requirements included the preservation of the adjacent park space and did not allow for new surface parking, the only option was underground parking. A 174-stall underground parkade would have substantially increased project costs and embodied carbon.
To address this challenge, the project team collaborated closely with a transportation consultant to implement transportation demand measures aimed at reducing parking requirements. The project includes enhanced provisions for active, public, and alternative forms of transportation which support the projects goals of equitable access to community facilities. This strategic design approach resulted in a reduction of parking stalls – from 174 to 100, resulting in substantial cost savings and the biggest embodied carbon reduction of all reduction strategies.
4. Collaborate with Construction Managers

Various options for each structural component were evaluated based on cost, layout efficiency and embodied carbon. Heatherbrae Builders, the construction management firm, was heavily involved in the mid-design stage to advise on the constructability of the design.
An innovative procurement process was used to evaluate the cost-effectiveness of the design team’s embodied carbon reduction strategies. The process consisted of having the general contractor provide a baseline bid alongside an alternate bid for the lower-embodied carbon options. The embodied carbon of alternate products had to be proven using environmental product declarations (EPDs). The project team used an embodied carbon tracking form that helped the client make decisions based on the cost effectiveness of the embodied carbon reduction strategies.
5. Specify Low-Carbon Insulation for Passive House Performance

Because the project is pursuing Passive House certification, the building’s thermal envelope has a continuous layer of insulation. For a fair comparison, both the baseline and proposed designs incorporated identical insulation in terms of location and thermal performance, but the type of insulation varied. Due to fire code and climate resilience considerations, there were few alternatives to mineral wool for the walls and some roof areas. However, significant embodied carbon reductions were achieved for rigid insulation. Soprema Sopra XPS was specified as the only acceptable rigid insulation due to its very low embodied carbon. This reduced the embodied carbon by 143 tCO2e compared to the baseline while maintaining Passive House levels of energy efficiency.
By combining the design measures, the project is on track to meet the 40% reduction in embodied carbon goal.
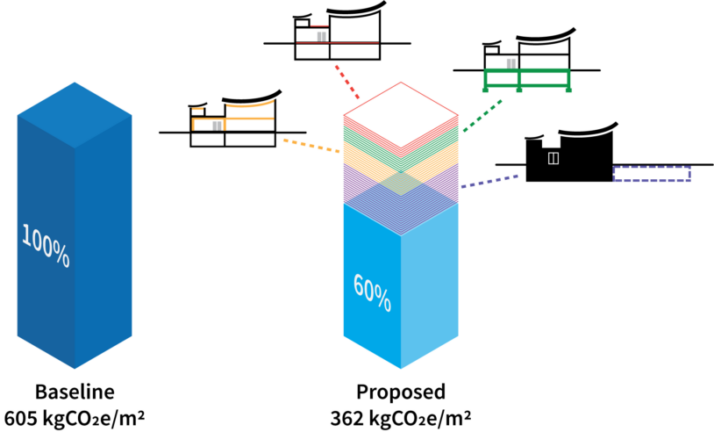
Embodied carbon reductions resulting from deleting a portion of the parkade (purple), mass timber structure (yellow), low-carbon concrete (green) and low-carbon rigid insulation (red).
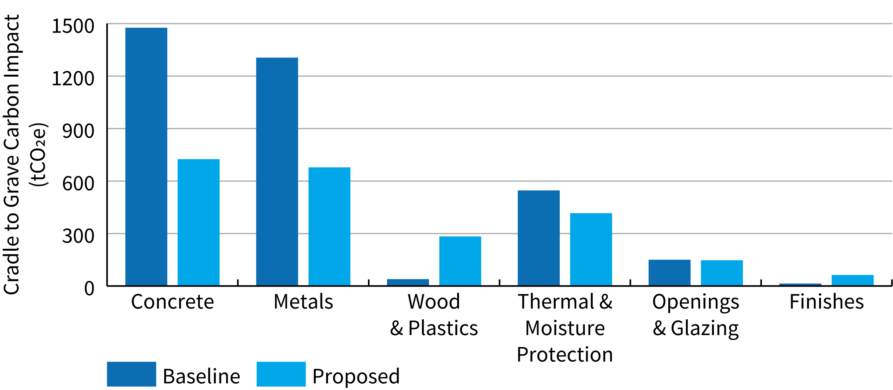
Embodied carbon breakdown by material type
The Complete Carbon Picture
The project’s ultra energy efficient envelope, required for Passive House certification, paired with efficient mechanical systems fueled by BC’s clean electricity grid, reduced the building’s modelled greenhouse gas emissions to approximately 3.5 tCO2e/year or 0.6 kgCO2e/m2/year (the highest step of the Zero Carbon Step Code). As a result of this extremely low level of operational emissions, the upfront embodied carbon constitutes the lion’s share of the building’s total carbon footprint over 60 years.
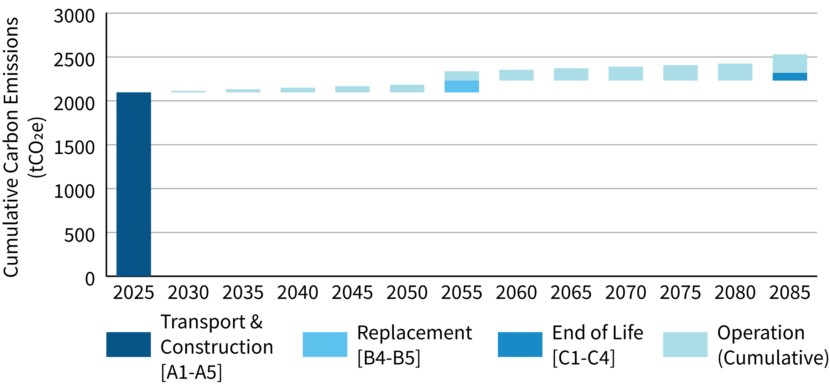
Comparing the building’s projected operational emissions with its embodied carbon emissions
Achieving 2030 Targets Today
The project began construction soon after the official sod-turning event in November of 2023 and occupancy is scheduled for early 2026. As construction progresses, the project team is continuing to ensure that targets are met through a rigorous submittal review and reporting process. The project’s embodied carbon analysis will culminate with an as-built whole-building life cycle assessment.
Although the City is aiming for an embodied carbon reduction of 40% by 2030, the Marpole Community Centre has proven that it can be achieved today.