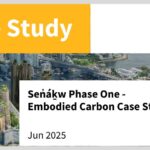
Sen̓áḵw Phase One – Embodied Carbon Case Study
June 9, 2025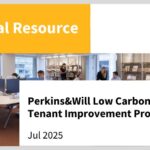
Perkins&Will Low Carbon Tenant Improvement Project
July 10, 2025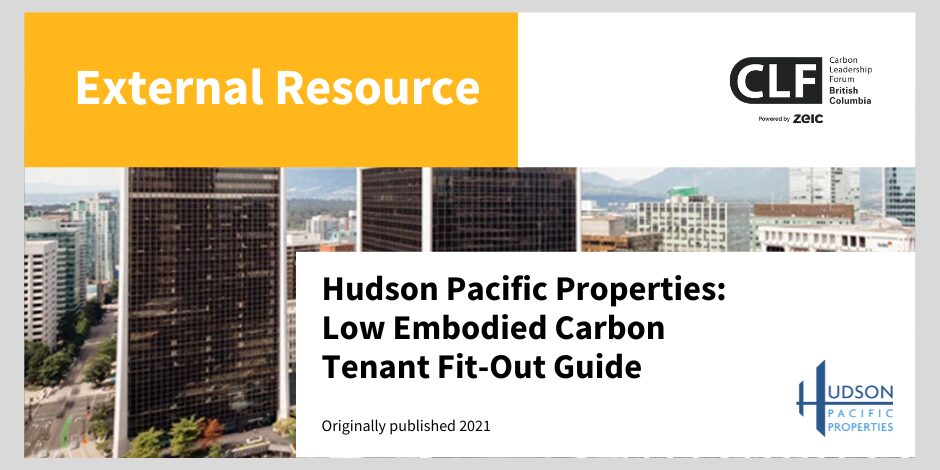
Commercial office landlords have a unique ability to drive sustainable behavior change at scale. Hudson Pacific Properties has developed this guide to share their learnings and give their tenants insight and guidance when considering lower carbon materials in office fit-outs. By implementing the strategies presented in this guide, you can reduce your carbon footprint with minimal impacts on budget and schedule, providing a win-win for your organization and the environment. The guide demonstrates that low‑carbon tenant fit‑outs are not only feasible, but they can be cost‑effective and replicable. Incremental improvements in material choice and specification, supported by digital tools and proactive procurement, make it possible to significantly reduce embodied carbon in interiors across commercial properties, contributing meaningfully to broader climate goals.
The guide features a Vancouver case study, HPP's Bentall Centre, to demonstrate how low-carbon strategies can be applied in real-world tenant spaces. By implementing a set of low-carbon material substitutions, the project achieved a 32% reduction in embodied carbon, bringing it down to 258 kg CO₂e/m².
Key Principles & Benefits
- Set early embodied carbon goals and integrate them during the design and procurement phases.
- Use quantitative tools (e.g. EC3, LCA software) to track and benchmark embodied carbon for tenant fit‑outs.
-
Recognize that interior renovations, typically occurring every 10 – 15 years, can cumulatively contribute embodied carbon nearly equal to the structure over a building’s lifespan.
- Prioritizing low‑carbon materials doesn’t mean higher cost; HPP data show material substitutions often carry minimal to zero premium, and may even cost less due to reduced cement content, modular design, or steel reuse.
- Supporting tenants in low‑carbon choices can enhance brand reputation, sustainability credentials, and readiness for emerging regulations.
Material-Specific Strategies
- For concrete and cement, optimize mix designs (e.g. use supplementary cementitious materials) and relax curing schedules (e.g. 56-day strength) to reduce embodied carbon by up to 33%, often at low or no added cost.
- For steel and rebar, specify a high recycled content and steel produced via electric‑arc furnaces on clean grids. This can reduce embodied carbon by about 4 – 10%, again with minimal cost impact.
-
Choose low‑GWP insulation (mineral wool, plant‑based, cellulose) instead of XPS, cutting embodied carbon significantly (about 16%).
- For finishes like carpet backing, ceiling tiles, or paints, choosing low‑carbon finishes can reduce embodied carbon by about 5% with little to no added cost.
- Use low‑carbon glass/frames where possible. It can lower embodied carbon by about 25% but tends to add about a 10% cost premium.
Recommendations for Tenants & Owners
- Integrate embodied carbon requirements into tenant criteria, procurement, and RFPs.
- Request EPDs (Environmental Product Declarations) for key materials to assess carbon impact.
-
Use EC3, LCA, and BIM tools to quantify embodied carbon in fit‑out packages across standard tenant areas.
- Collaborate with landlords, designers, and contractors to benchmark, set targets, and monitor carbon performance.