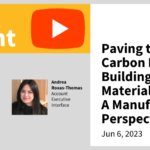
Paving the Way to Carbon Negative Building Materials: A Manufacturer’s Perspective
June 6, 2023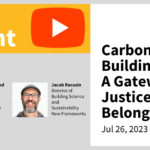
Carbon Storing Buildings: A Gateway to Justice and Belonging
July 26, 2023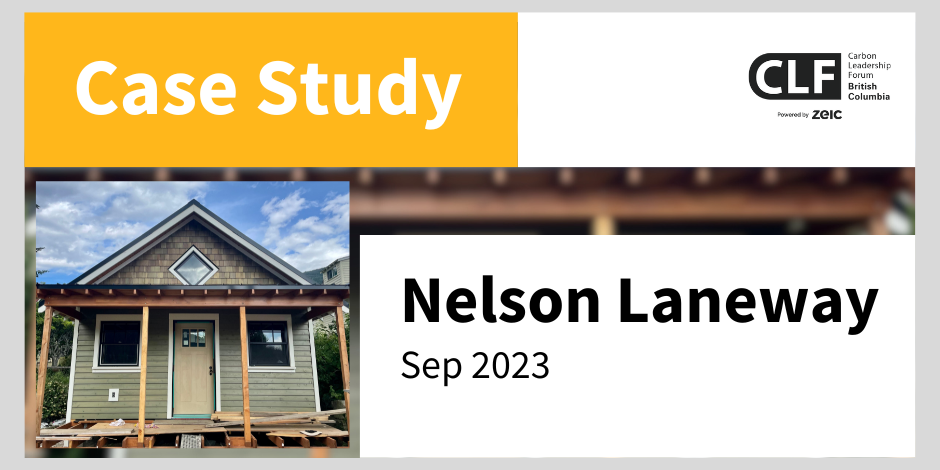
Summary
Reducing the whole-life carbon of buildings is crucial to meeting Canada’s 2030 and 2050 climate goals. Currently, buildings in BC alone are responsible for about 15 megatonnes of carbon annually [1]. To counter this, national and provincial regulations are increasingly setting stringent requirements for home efficiency and building energy use. However, even with this progress, the material emissions associated with constructing a building will continue to be a dominant source of carbon emissions. As an illustration, the carbon emissions associated with constructing a home in BC can be as much as 30 years’ worth of operational emissions or up to 250 years’ worth of operational emissions for all-electric homes [2].
The Vancouver Building By-Law recently adopted embodied carbon limits for Part 3 (large, multi-storey, or significant) buildings, but right now there are no embodied carbon limits for homes. By publishing this case study, CLF British Columbia hopes to bring awareness of this issue to the low-rise building industry and to highlight that emissions can be dramatically reduced without adding costs to construction.
In 2021, the City of Nelson conducted a study in collaboration with Builders for Climate Action as part of Phase I of their Low Carbon Homes Pilot. [2]. They found that the embodied carbon associated with building a home in Nelson1 varied from as low as 71 kg CO2/m2 all the way up to 309 kg CO2e/m2. Similar reports conducted in other Canadian cities by the same authors report similar findings [3,4].
In this case study we explore how one builder in Nelson achieved a Material Carbon Intensity (MCI = total material carbon emissions / heated floor area) of just 20 kg CO2e/m2.
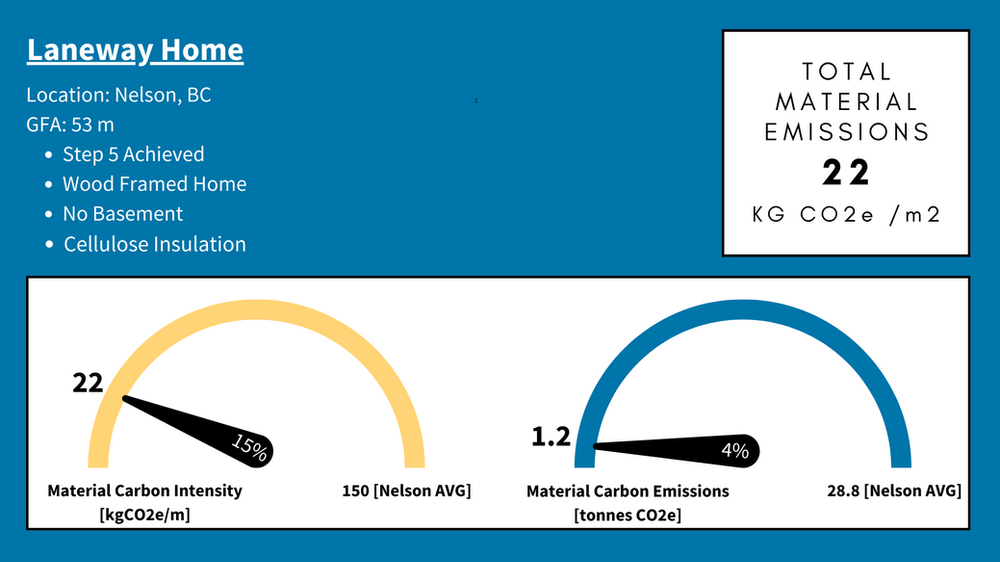
Introduction
Mike Coen, Founder of Build Environmental in Nelson BC wanted to build a laneway house with the smallest carbon footprint possible. The goal was to minimize both embodied and operational emissions. Working with Harmony Engineering, they were able to deliver a project that became emblematic of the City of Nelson’s work to reduce embodied carbon in the community.
Mike had been working in the construction industry for over a decade, with significant experience building “traditional” homes. However, this laneway was the first home he designed and built for himself. As someone deeply committed to sustainability, he wanted to minimize his carbon footprint to be a central feature of his laneway house project.
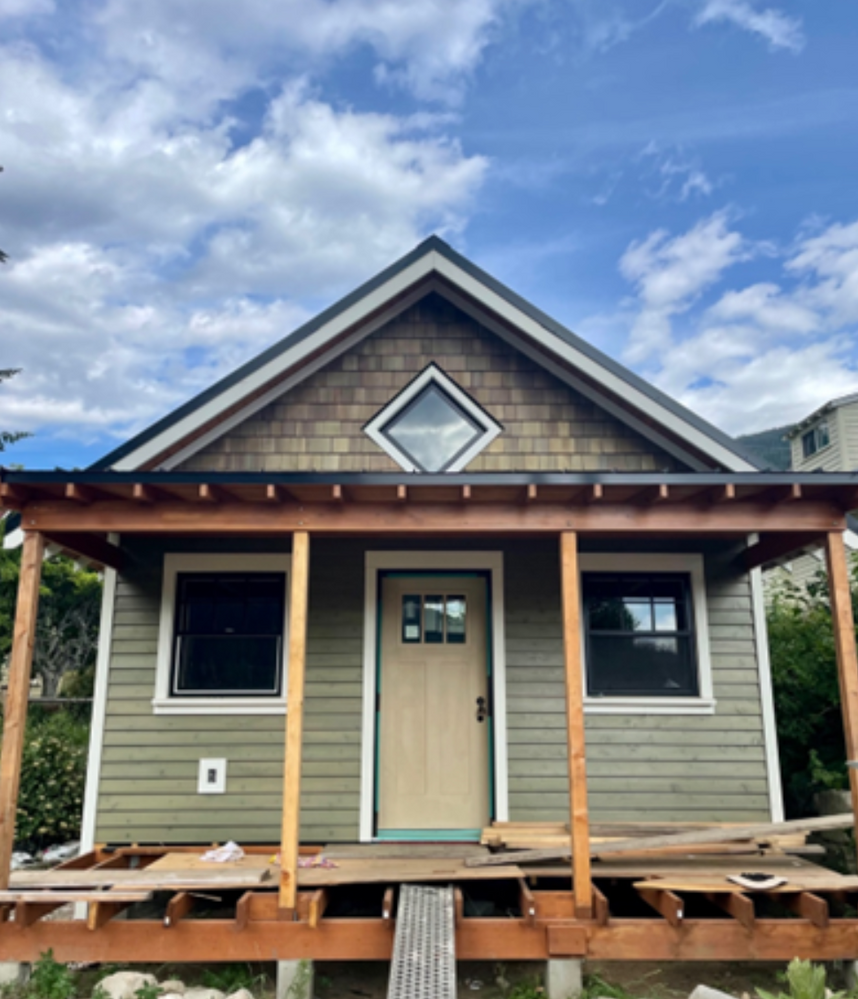
Mike focused on minimizing both operational and upfront carbon in order to reduce his carbon footprint as much as possible. Although upfront carbon (embodied carbon) was new territory for Mike, he quickly realized this was where he could have the biggest impact. However, since an energy-efficient home was the end goal, Mike also had to balance the requirement for increased insulation alongside his desire to minimize upfront emissions.
In building the laneway, embodied emissions are calculated using the BEAM Estimator. This is an Excel-based material carbon emissions estimator, designed for use in residential buildings. BEAM calculates emissions based on life cycle stages A1– A3; in other words, the emissions reported are associated with material production as reported in the Environmental Product Declarations (EPDs). BEAM uses a mix of product-specific and industry average EPDs as the availability of EPDs dictates. In this case study we are focusing on upfront emissions and include the contribution from carbon sequestration of fast-growing crops and recycled wood products.
Low Embodied Carbon Design
The laneway is a traditional style, two-storey, stick frame building that is all electric and designed to meet the requirements of Step 5 of the BC Energy Step Code. Mike was able to modify typical home construction details to suit his low-carbon pursuit with changes designed to minimize the carbon footprint. He used three key strategies to reduce the upfront carbon emissions, resulting in almost 20 t CO2e in carbon savings.
1. Eliminate the Basement
The embodied carbon of a basement is typically four times the embodied carbon of above grade floor space. The material volume required to enclose a basement, resist ground pressures, and incoming water is large; basement walls can be more than 300 mm thick. This is a lot more material than you’d need to build an above ground space.
Due to its waterproof nature, basements are almost exclusively built out of concrete. Since the embodied carbon associated with concrete is significantly higher kilogram for kilogram than for wood, using concrete expansively, to cover walls or ground, is not an efficient use of this carbon-intensive material. Eliminating the basement also saves material costs, excavation costs, and the need for waterproofing, as well as decreasing overall build time.

2. Eliminate Concrete
Beyond the basement, one of the project’s goals was to eliminate as much concrete as possible. Typical construction involves a concrete ground floor slab as well as concrete strip and pad footings. Concrete strip footings are usually continuous and without detailed design. They often use much more concrete than is necessary to transfer loads to the ground. In this laneway, concrete pier foundations were used in lieu of continuous concrete footings. These vastly reduced the amount of material needed to support the building. Furthermore, the pier-type foundation allowed for a suspended wood-framed ground floor slab and eliminated the need for a frost wall.
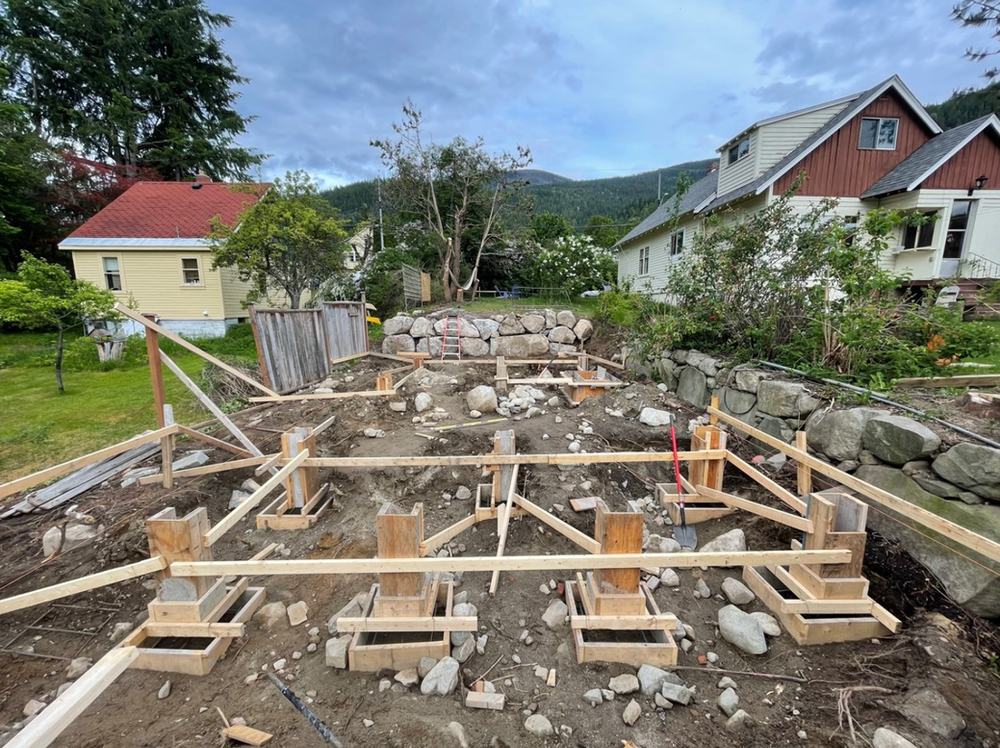

3. Carbon Storing Envelope
In the design of this laneway, locally sourced cedar siding was used in place of metal or fibre cement siding. As a slow-growth forestry product, carbon sequestration is not included in the upfront material emissions of the cedar siding. However, as a minimally processed product, the upfront emissions of cedar siding are significantly less than traditional alternatives.
In addition to the siding, dense-packed, carbon-storing cellulose was used to insulate the walls. A typical wall assembly built in Nelson would be 2×6, with fiberglass batt insulation and R6 comfortboard (mineral wool) exterior insulation. The end result is a thermal bridge-free R26 wall. In this laneway, dense packed cellulose was used in combination with a 2×8 staggered stud to eliminate thermal bridging. This not only achieved R26 wall assembly but saved more than a tonne of carbon emissions.
In addition to the carbon savings from choosing locally sourced materials, there are also savings in emissions due to transport. This laneway achieved Step 5 on the BC Energy Step Code; it is rated as net zero energy ready.
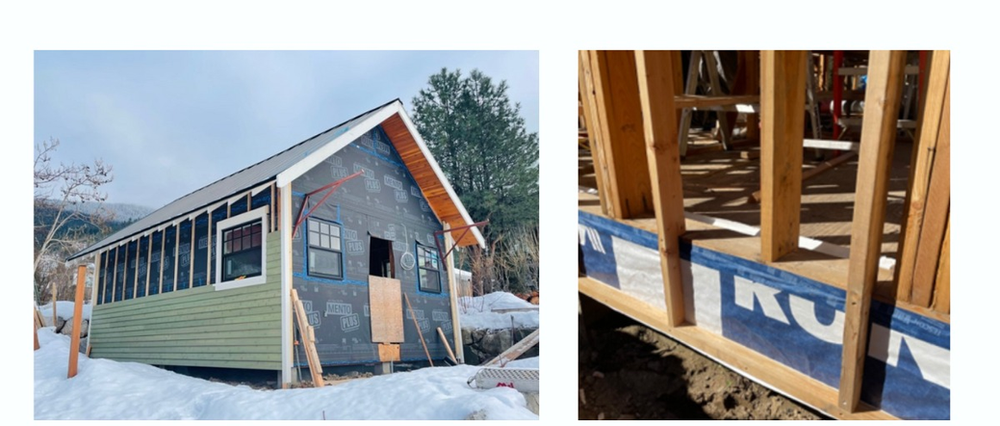

Comparison
This laneway has shown that significant carbon savings are possible with just a few key changes. Although not standard, none of the substitutions used here are particularly drastic or require a change in the way we build; and all are possible within part 9 of the BC Building Code. In addition to carbon savings, the laneway was also built more quickly and at a lower cost compared to a typical Nelson home. The Nelson Laneway project has an Material Carbon Intensity (kgCO2e/m2) – a metric that allows buildings of various sizes to be compared – is 91% smaller than the average new single detached home built in Nelson. It is also 96% smaller than average new home constructed in the city, which highlights the importance of minimizing the square footage where appropriate. Avoiding excessively large floorplates and finding ways to use building materials more efficiently can not only reduce emissions but can also reduce overall cost and building time.
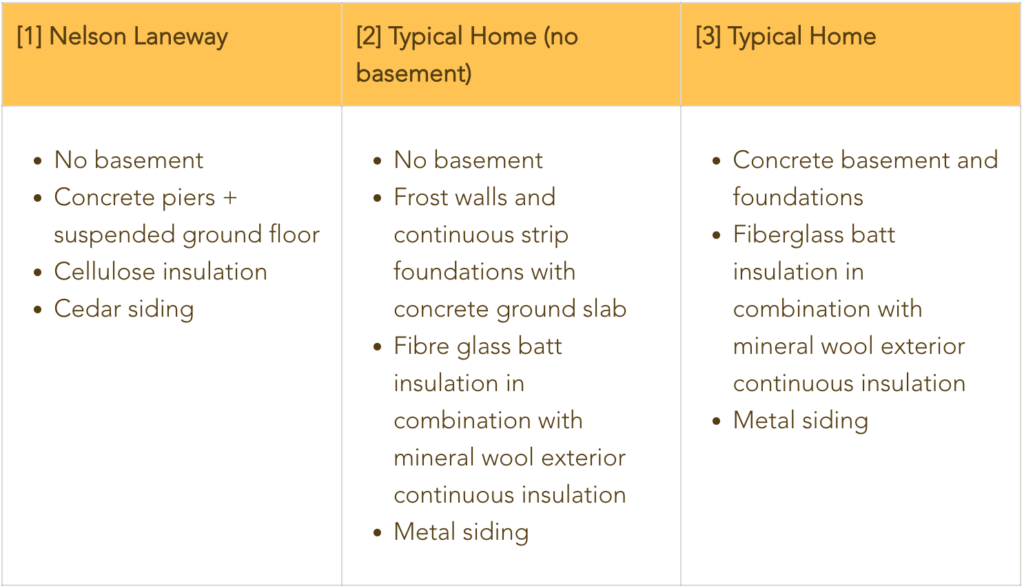
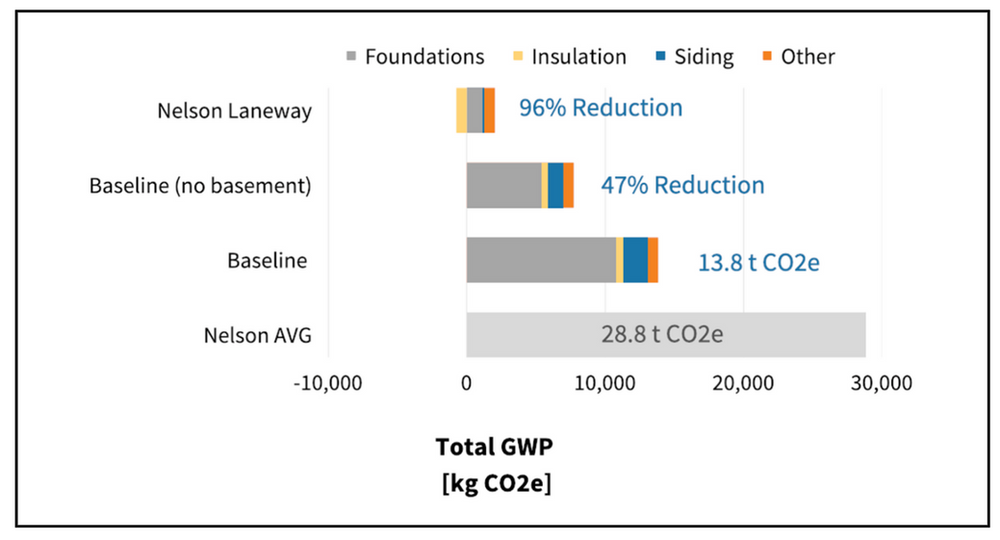
Prior to building this home, Mike had very little experience in low embodied carbon design. All of the strategies used here were simple to incorporate, easy to build and led to overall cost savings in addition to reducing the carbon footprint. By eliminating the basement, and using pier footings and a suspended slab, Mike estimates that he saved $25,000 in material costs, and reduced construction time by a substantial 14 days.
The two biggest challenges in construction were the double stud wall and developing a solution to prevent grade level pipes from freezing. Mike estimates that the double stud solution for the wall added approximately one additional day of construction and provided an insulated ground level concrete chase for the piping. Both solutions cost less than $1000 in additional materials.
Basements are often included as standard throughout BC, as mechanical space, additional rental income, or just additional space; however, basements are resource intensive, and both design teams and clients should consider whether there are alternative, above-ground solutions to their space needs. Often excavation is necessary to place foundations below the frost level, this pier foundation solution eliminated that need.
Low carbon design does not need to be an exercise in sourcing expensive materials, and it doesn’t need to involve significant changes to the design. Being mindful of resources and using materials effectively and efficiently can both reduce carbon emissions. The design of this laneway showed that 70 percent of the carbon footprint could be slashed without resorting to more expensive products.
Key Lessons
- Embodied carbon savings do not need to cost more.
- Concrete basements can contribute up to 60-70% of the total carbon footprint of a home; reducing or eliminating basements from the design would allow us to meet 2030 climate targets today.
- Carbon-storing materials are a great way to lock carbon sequestered from fast growing crops into homes for a significant period. For our stance on carbon sequestration, see the definitions below.
- High-performance homes do not equate to high embodied carbon homes.
References:
[1] Embodied Carbon Modelling Study, Priopta 2023, Carried out for the province of BC, accessed JAN 2023: https://www.priopta.com/downloads/bc-embodied-carbon-modelling-study
[2] Nelson Benchmark Study, Builders for Climate Action, carried out for the Cities of Nelson and Castlegar; accessed JAN 2023: https://www.buildersforclimateaction.org/our-work.html
[3] Vancouver Part 9 Material Emissions Benchmark Report, Builders for Climate Action, carried out for the City of Vancouver, accessed Mar 2023, https://www.buildersforclimateaction.org/uploads/1/5/9/3/15931000/vancouver_part_9_material_emissions_benchmark_report_ammended_nov_222022__1_.pdf
Appendix: Key definitions
Embodied carbon: In this report, emissions stated are those associated with life cycle phases A1-A3 i.e., the material production emissions only. The assessment of this home was carried out using the Builders for Climate Action tool BEAM, which has assessments upfront, or cradle-to-gate emissions only. There is a time priority associated with carbon emissions; although considering A1-A3 does not paint the fullest picture, it does allow us to accurately compare the emissions being created today, our most critical decade for CO2 reductions. Further information on the time importance of carbon can be found here: https://carbonleadershipforum.org/the-time-value-of-carbon/
Materials: in this report, the word “materials” is loosely used to mean the individual components that go into building a home, whether that’s an actual material, like wood or steel, or a component like a cladding panel that is made up of a group of materials.
Carbon Storing Materials: our position on carbon-storing materials aligns with that of Builders for Climate Action, and is incorporated within their BEAM tool. We do not advocate for including sequestration values for virgin forestry products. Within this case study, carbon storage is considered for fast-growing crops, or from recycled forestry products only. For more information see the BEAM User Guide, accessible via https://www.buildersforclimateaction.org.