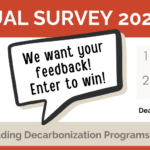
Building Decarbonization Programs: Annual Survey 2024
June 27, 2024
Embodied Carbon in Vancouver Building Bylaw 2025
July 9, 2024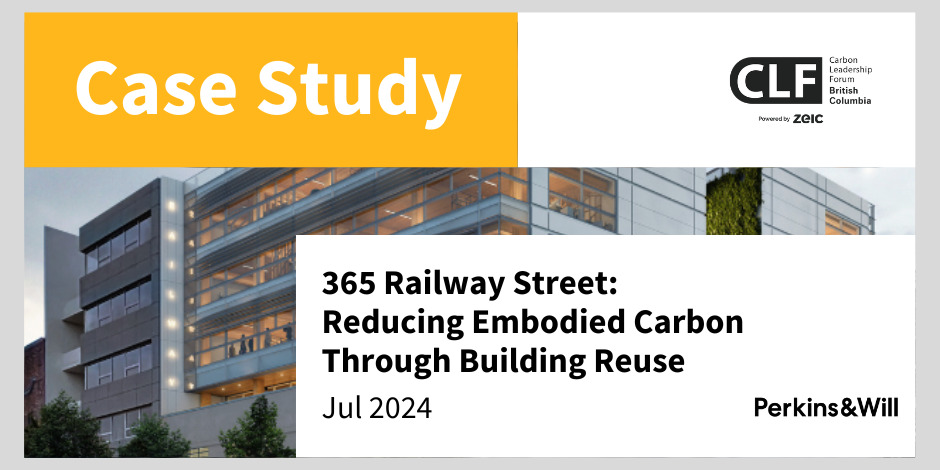
Written by Amy Brander, Kathy Wardle and Aaron Knorr of Perkins&Will.
All photos and images are courtesy and property of Perkins&Will.
This project is targeting CaGBC’s Zero Carbon Building (ZCB) Design StandardTM (v3) and LEED Gold (Building Design and Construction: Core and Shell) certifications. It was the winner of the inaugural 2023 BC Embodied Carbon Awards (Large Buildings in Vancouver category) and has the lowest embodied carbon profile of any project produced by the Vancouver Studio of Perkins&Will.
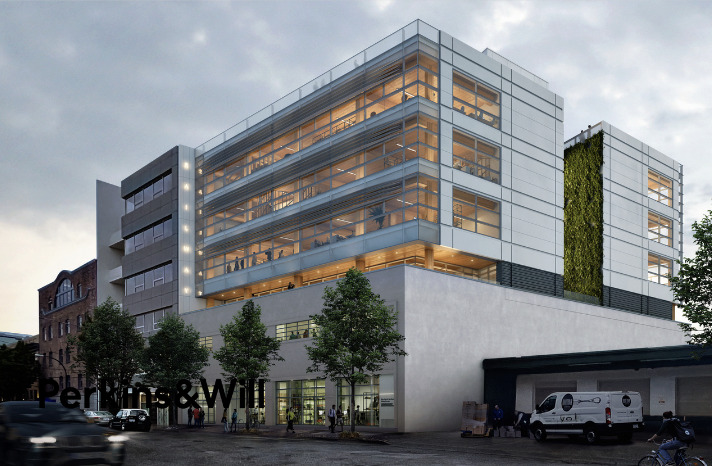
Why is Embodied Carbon Important?
As we design more energy-efficient buildings, embodied carbon – the emissions associated with manufacturing, transportation, installation, maintenance, and eventual disposal of building materials - becomes ever more important to address. In British Columbia, where buildings are connected to a clean, low-carbon electrical grid, the embodied carbon can represent a major portion of a building’s overall carbon footprint.
When designing to reduce embodied carbon, an important consideration is the hierarchy of design measures and their relative impact on embodied carbon.

Embodied Carbon Reduction Hierarchy
- Reusing existing buildings instead of constructing new ones avoids the need to extract raw materials from the earth and manufacture new building products and materials, both of which are carbon-intensive processes.
- Efficient design to reduce material volume and waste reduces the quantity of products and materials required to construct a building.
- Specifying materials and products with a low global warming potential (GWP) contributes to the reduction of the building’s overall embodied carbon.
This hierarchy guided many of the design decisions made for the 365 Railway project.
Project Partners
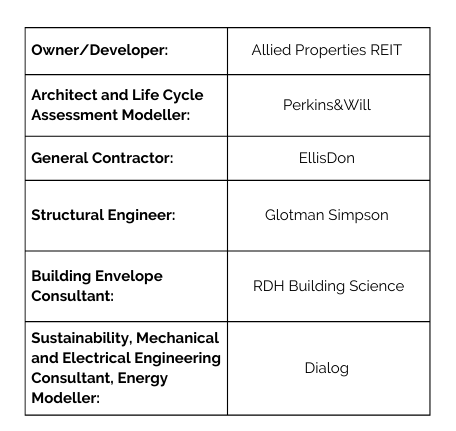
Key Takeaway: An iterative LCA process enables a design team to understand embodied carbon reduction potential and impact of design measures.
The Design Approach
The 5,950 m2 (64,000 ft2) redevelopment consists of a four-storey office addition to an existing two-storey building known as the Fleck Brothers Warehouse. An objective of Allied was to ensure the Fleck Brothers Warehouse was added to Vancouver’s Heritage Register to recognize the value of the building and its retention.

Fleck Brother Warehouse
This historic Vancouver building is a Late Modern-style warehouse constructed in the 1940s. The existing building has the structural capacity to support an additional three-storeys of concrete structure and as such, the developer set out to maintain the base structure as close to its original form as possible. From the outset, Allied had a clear mandate to prioritize the reuse and revitalization of the heritage structure with the ultimate goal of reducing the overall carbon profile of the project.
Phillip Armstrong, Director of Development, AlliedThe Railway redevelopment is the first Allied project to focus on achieving net zero carbon designation. While net zero projects often come with additional upfront capital costs, there is intrinsic value in the final product. When it comes to reducing embodied carbon, Allied’s redevelopment strategy is uniquely positioned for success because of our commitment to sustaining the history of the buildings we own by preserving rather than demolishing. The Railway project is important in the supporting future adoption of zero carbon within other Allied projects.
The building form is kept simple with the addition of a four-storey wood structure stacked on top of the existing building and aligned with the original structural grid below. The existing building is constructed of cast-in-place concrete, and the addition will be constructed of lightweight mass timber and a building envelope primarily consisting of curtain wall. Inside the existing building, the freight elevator and stair cores will be removed and replaced with a new core to upgrade the seismic performance and improve accessibility. The existing mechanical and electrical systems will be replaced with new energy-efficient systems.
Key Takeaway: Commitment, collaboration, and proactive discussions with clients, design team members, trades, and suppliers are vital to moving the industry toward low-carbon solutions.
Achieving a 45% Reduction in Embodied Carbon
During the schematic design phase, Allied established a goal of obtaining CaGBC’s ZCB Design Standard certification. This standard sets performance requirements for carbon, energy, impact and innovation. Allied tasked Perkins&Will to track embodied carbon in alignment with the ZCB standard. An absolute value of 350 kgCO2e/m2 of embodied carbon was established as an early goal. In addition to the ZCB requirements, Perkins&Will sought to understand the benefits of retaining and rehabilitating the existing structure to reduce embodied carbon.
Ongoing tracking and reporting of embodied carbon was performed by Perkins&Will through life cycle assessment (LCA) modelling during the design phase. This allowed the design team to identify and reduce the quantity of construction materials with the highest global warming potential (GWP). Biweekly, hour-long sustainability meetings were held throughout the design phase to ensure the project was on track to meet the ZCB requirements. During these meetings, updated LCA and energy modeling data was reported and strategies to reduce carbon were explored by the project team. Using this collaborative and interdisciplinary approach to coordination, embodied and operational carbon were considered alongside aesthetics, constructability and cost, and carbon reductions were prioritized.

The most recent LCA results corresponding to the Issued for Tender drawings indicate that the embodied carbon of the project is less than 350 kgCO2e/m2 for modules A to C of the LCA. Modelling was performed in compliance with the ZCB standard and excluded biogenic carbon sequestration. The results of the study showed that reusing the existing building contributed 29% to the embodied carbon reduction. The reduction in material volume and specification of low-carbon building materials contributed an additional 16% to the embodied carbon reduction. These three design measures resulted in a 45% reduction in embodied carbon relative to the baseline for the project.
Key Takeaway: An early, clear and lasting client commitment and focus on reusing and improving existing buildings is critical to reducing embodied carbon in the building sector.
Optimizing Material Use
EllisDon, the project’s General Contractor, was engaged during the design phase to identify low-carbon construction products and materials. They reached out to their network of suppliers to ensure that the theoretical reduction in embodied carbon could be achieved during the construction phase.
The following key embodied carbon optimizations were prioritized and implemented by the design team:
Timber Optimization
By using a lightweight timber structure comprising of glulam columns and cross-laminated timber (CLT) floors for the addition, the design team was able to maximize the floor space and structural efficiency of the additional storeys on top of the existing building. This reduced the extent of upgrades or modifications to the existing concrete structure. Most of the composite timber elements will be prefabricated off-site to eliminate material waste and simplify the installation process during construction.
The interior of the new timber structure will be exposed. Showcasing the warmth and beauty of the wood will enhance the biophilic connection for the occupants. It also negates the need for additional interior finishes thereby reducing cost and material volume.

Project Interior View
Concrete Optimization
Concrete topping will be added to the suspended floor slabs. The roof structure will consist of cast-in-place concrete. Low-carbon concrete with a GWP of 10% below the British Columbia regional average (which is already approximately 30% lower than the Canadian average) is specified for all concrete mixes. This should result in a reduction of approximately 30 kgCO2e/m2.
Insulation Optimization
Expanded polystyrene insulation (XPS) will be used below the new slab-on-grade and for the roof insulation. It was originally chosen for its durability and compressive strength, but during the LCA analysis, it was found to be a carbon-intensive material in comparison to bio-based or mineral wool insulations. As a result, the quantity of XPS insulation below the slab-on-grade was reduced and low-carbon XPS insulation was specified for all applications. The XPS must come from suppliers that can provide Environmental Product Declarations (EPD) with product-specific and verified GWPs.
Key Takeaway: Reducing carbon should be intrinsic to every aspect of design.